Technology to form a linear movement actuator–with high contraction similar to the level of human muscle–created with a bundle of flexible, lightweight shape memory alloy springs that demonstrates strength dozens of times the human muscle to be applied on linear stage, robot, etc.

Client / Market
- Industrial, service robot companies
- Wearable robot companies
- Linear stage companies
- Small linear actuator companies
Necessity of this Technology
- Existing motor type actuator needs to be combined with a reducer, which increases the total mass and volume of the robot. It makes noise and is very dangerous when collided with human.
- There is a need for noiseless, high-power, high-contraction artificial muscle module that is light and flexible as human muscle but able to generate tens of times more force than human muscle and can move beyond the limits of human muscle.
- Unlike heavy, solid motor-based on rotary motion, linear contraction-expansion motion like skeletal muscles
- Enables designing a safe, lightweight robot, which can be applied for industrial robots and home service robots for cooperation with human and utilized for industrial uses
Technical Differentiation
- Artificial muscle dozens of times stronger than human muscle, formed with a bundle of shape memory alloy springs
- Adopts heating/cooling method using hot water and cold water to enable fast operation (0.5 Hz to 1 Hz or higher)
- Shape memory alloy spring bundle is covered with highly elastic tube. Using the automatic water temperature control valve, supply water of appropriate temperature to operate the artificial muscle and demonstrate specific strength.
- Contraction with the simple method of supplying current
- Inductance changes as the shape memory alloy spring bundle contracts and expands and cause the length to change.
- Additional displacement sensor is unnecessary as the artificial muscle length is measured this way.
- Small operational noise (noiseless, low noise operation)
Excellence of Technology
- The mass of the bundle containing 24 shape memory alloy springs is only 10 g, but it can lift a 10 kg load at 56% contraction rate.
- The length of shape memory alloy spring artificial muscle in low temperature is 133 mm and 58 mm in high temperature.
- Power density of over 1,500 W/kg and contraction rate over 40% at the operation speed of 0.5 Hz
- Force-displacement control of the artificial muscle using automatic water temperature control valve
- When the artificial muscle is applied on robot arm, the robot can lift up and down a 2 kg dumbbell at the speed of 0.5 Hz or higher repeatedly.
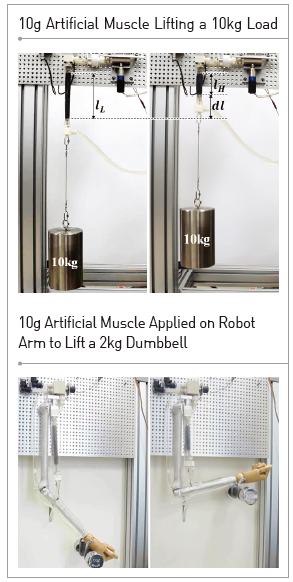
Current Intellectual Property Right Status
PATENT
- Artificial Muscle Module (KR1696880)
- Artificial Muscle Module Equipped with Displacement Measuring Device (KR1731491)
- Shape Memory Alloy Spring Manufacturing Device and Method (KR1712958)
- Artificial Muscle Module Using Shape Memory Alloy and System Including the Module (KR1827312)
- Artificial Muscle Module, Artificial Muscle Module Manufacturing Method and Artificial Muscle Module Control System (KR1827815)
- Artificial Joint System and Control Method (KR1827817)
KNOW-HOW
- Shape memory alloy spring mass production technology
- Automatic water temperature control valve technology
- Shape memory alloy spring strength-placement control technology
- Sensorless displacement measurement technology using shape memory alloy spring only
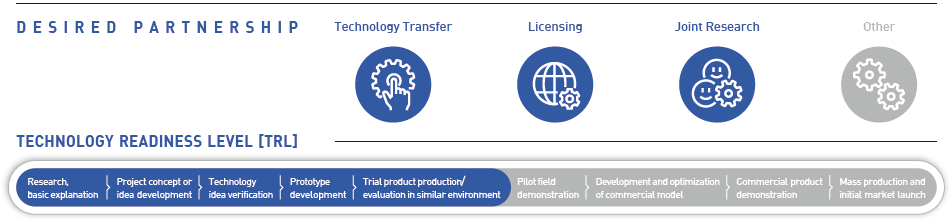 |