Semi-active damper that reduces the vibration from drive train by
controlling the vertical shock of the wind turbine gearbox using a
hydraulic chamber and damping controller
Client / Market
- Wind turbine manufacturer
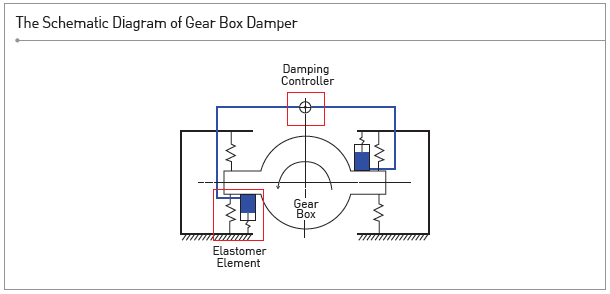
Necessity of this Technology
- Existing technology uses a hydraulic cylinder for effective control of vertical
movement of the wind turbine gearbox at a specific excitation frequency and cannot
effectively respond to another excitation frequency when it suddenly enters.
Technical Differentiation
- Since the variable damping coefficient can be adjusted even if the excitation
frequency flowing from outside is changed, the variable damping coefficient that
minimizes the vertical displacement due to the disturbance of the hydraulic cylinder
is detected and the vibration is controlled.
- It is a semi-active damper that automatically controls the change of flow rate due to
hydraulic disturbance in passive damper using a commonly used hydraulic cylinder.
Excellence of Technology
- As shown in the figure blow, the elastomer consists of hydraulic chamber and a spring.
- There is one elastomer each below the left gear box arm and above the right gear
box arm, and the two are connected through a hydraulic line with the damping
controller in the middle of the hydraulic line.
- Rotational torque occurs in the gear box from the blade rotation of the wind turbine,
and the force from the rotational torque tries to change the volume of the hydraulic
chambers on both sides by the same amount, but the hydraulic chambers are
connected through the hydraulic line, therefore, the balance of the force is maintained
to suppress the rotary movement of the gear box and only allow vertical movement.
- As the gear box moves upward, the volume of the hydraulic chamber above the
right arm decreases, and the volume of the hydraulic chamber below the left arm
increases.
- Here, the oil moves through the hydraulic line, and damping force occurs from the
movement of the liquid.
- On the contrary, when the gear box moves downwards, the same damping force is
generated.
- Therefore, the damping force generated from the oil flow reduces the vertical
vibration of the gear box.
- Also, with the damping controller in the middle of the hydraulic line, the oil flow is
controlled to adjust the size of damping force, and the gear box vibration can be
reduced effectively.
- The senior researcher has 30 years of research experience in vibration analysis and
control for highspeed rotary machine and reciprocating machine system.

CURRENT INTELLECTUAL PROPERTY RIGHT STATUS
PATENT
- Apparatus for Dissipating Vibration Energy (KR1437362)
- Damper and Generator Damper (KR1437363)
- Torsional Vibration Damper (KR1073864)
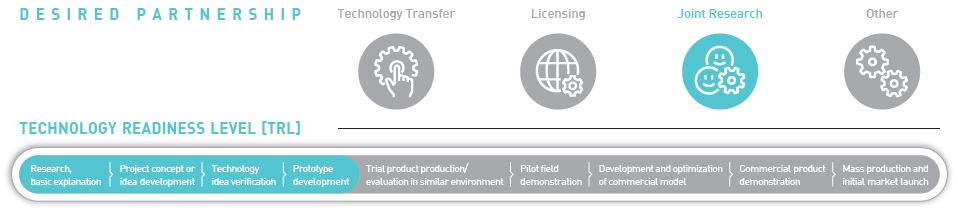
|