Thin-film thermoelectric module applicable for hot spot cooling and
as micro power supply
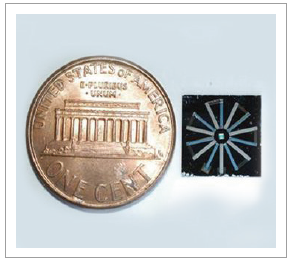
Client / Market
- Small portable power supply for WSN (Wireless sensor node), wireless electronics,
portable electronics, MEMS, wearable computer, cardiac pacemaker
Necessity of this Technology
- Micropelt of Germany developed a micro-thermoelectric module using Bi-Te thin
films and Bi-Sb-Te thin films and applied it as a power source of sensor node.
- Laird (formerly Nextreme) of the USA developed a micro thermoelectric module
that can be applied for hot spot cooling.
- GreenTEG of Switzerland developed a micro thermoelectric module and applied for
a heat flux sensor.
- Enhanced strength and reliability of the joint on thermoelectric legs are needed.
Technical Differentiation
- Thermoelectric thin films with power factor of 3.07 mW/K²m for Bi-Te films (N-type)
and 4.41 mW/K²m by Bi-Sb-Te films (P-type) are developed.
- The power output of thermoelectric module is 7.5 mW/cm² when the temperature
difference is 50 degrees.
- It can be used as a wireless sensor power source for monitoring systems used in
environments where battery replacement is difficult such as high temperature, high
pressure, underground, or high above the ground in intelligent plant, smart building,
transport machine, etc..
- It can be applied to hot spot cooling technology where demand for portable hotspot
cooling technology has been increased due to the recent slim and small size
of portable electronic products such as smartphones, tablet PCs, micro-packages,
and LED lighting.
- Secured core elementary technologies
- Thermoelectric module analysis and design technology
- Thermoelectric thin films deposition technology
- Thin-film thermoelectric module process technology
- Performance evaluation technology of thermoelectric thin films and thin-film thermoelectric module
Excellence of Technology
- Finite element analysis technique is used for design to determine the structure and
size of the thermoelectric module.
- Optimal deposition conditions for thermoelectric thin films using co-sputtering and
co-evaporating are secured.
- A measurement technology is developed to assess the performance of developed
thin-film thermoelectric module.
- A bonding process is developed with an exclusive jig designed and produced for
bonding process, and by selecting and evaluating the bonding materials and then
optimizing the bonding conditions.
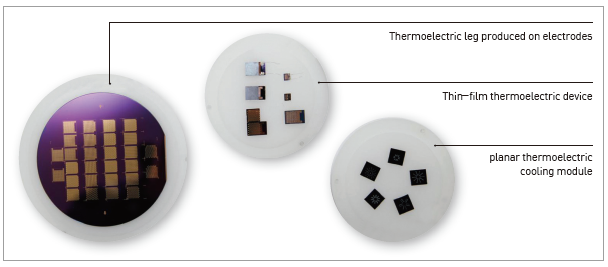
Current Intellectual Property Right Status
PATENT
- Thermoelectric Energy Conversion Module Having Spring Structure (KR1068647)
- Thin-film Thermoelectric Module Manufacturing Using Transfer Process (KR0984108)
- Method for Manufacturing the Thin-film Thermoelectric Energy Conversion Module (KR1068490)
- Method for Manufacturing a Thin-film Flexible Thermoelectric Module Using Peeling Process (KR0975628)
- LED Package Embedded with Thermoelectric Module (KR1004746, PCT/KR2010/009132)
- LED Package with the Function of Thermoelectric Cooling (KR1064870)
KNOW-HOW
- Analysis-based thermoelectric module design technology
- Thermoelectric thin films optimized deposition technology using vacuum deposition method
- Thermoelectric module manufacturing technology using thermoelectric thin films
- Cooling and power generation performance evaluation technology for thin-film thermoelectric module
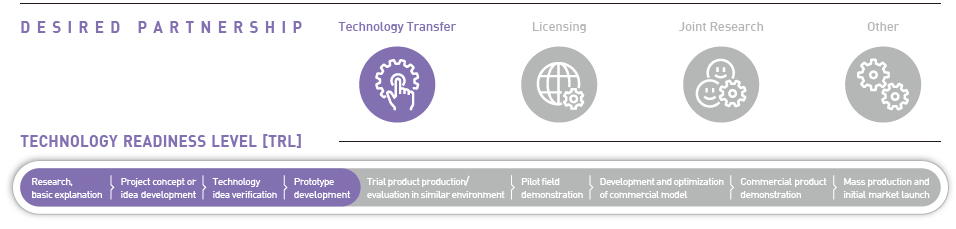
|