Reduce vibration and improve surface roughness through active
vibration proof during precise boring of a deep hole for large integral
structure (aspect ratio over 7D)

Client / Market
- Machining-tool manufacturer / Machine-tools manufacturer
Necessity of this Technology
- Vibration and low surface roughness intensity while boring a deep hole in a large
integral product is an issue.
- With the aspect ratio over 4D, it is difficult to secure surface roughness due to
vibration that the parts are processed with the module and then welded.
- Passive methods using damper or vibration proof machine are usually adopted, but
it cannot be used for a hole greater than 7D.
- Recently, deep hole processing has become frequent for a large integral product
(aircraft landing gear, large motor/display, wind power facility, etc.).
- In particular, boring process requires precision, and to secure surface roughness
(usually up to 2 μm), periodic damping (damping ration over 30%) is required during
the deep hole work.
- Active vibration proof technology is an alternative technology.
Technical Differentiation
- By measuring the vibration real-time using the adaptive active damping with antivibrating
of frequency of occurred vibration and offsetting such vibration (destructive
interference through deducting the main frequency and phase modulation of
frequency in possession), the accuracy of machine tool process work can be
improved, and the life of the machine tool can be extended by reducing vibration,
and these lead to a great cost reduction effect.
- Under the aspect ratio over 7D, precise boring of a large integral product can
be done with the roughness between 1.8 μm and 2.0 μm; since the process of
disassembling and welding back is no longer necessary, reduced number of
processed parts and frequency of processing lead to short processing time and
improved precision and productivity.

Excellence of Technology
- After the frequency and wave estimation stage estimating the main frequency and
wave using the vibration size and Fourier transform signal and measurement of
the actual vibration amplitude of the vibration source, the amplitude for destructive
interference is decided to actively control damping.
- Previously, the precision processing used a passive method of using vibration proof
machine or damper, but this method is the world’s first active method
- Five SCI-level papers related/based on the technology have been published (1
author) on JMST, IJPEM, and Key Eng.; over 20 years of research experience in machine
intellectualization field
- Received the 2012 Korea Society of Mechanical Engineers Baekbong Technology
Excellence Award, 2011 KIMM Academic Award, and 2007 ICROS Academic Award
Current Intellectual Property Right Status
PATENT
- Machine Tool Vibration Reduction Device and Method (KR1436984, PCT/KR2013/008236,
US14/128709, JP2014-539893)
- Detachable Active Vibration Proof Device and Method Using MR Vibrator and Piezo
Vibrator (KR1510638)
- Machine Tool Chatter Vibration Compensating Device (KR1015058)
- Active Vibration Reduction Device Using MR Fluid (KR1321468)
KNOW-HOW
- Active vibration-control based machining technology for large integral product
- High-speed precision boring processing and active chatter vibration reduction technology
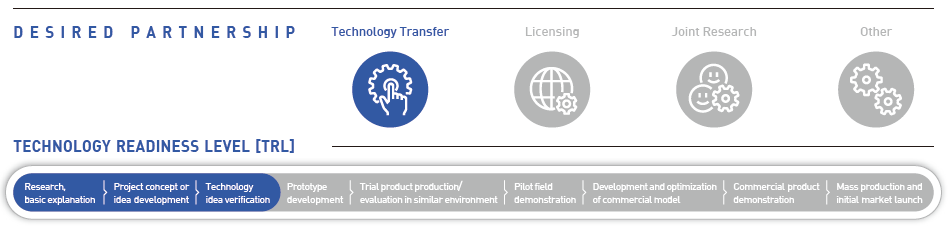
|