Chuck holder built-in machining origin for unmanned machining setup process
Automatic identification and simultaneous autonomous control module
Client / Market
- Machining-tool manufacturer/Machine-tools manufacturer
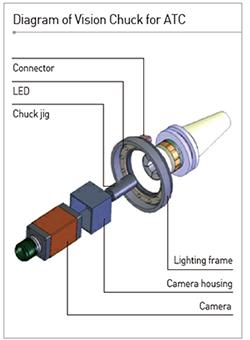
Necessity of this Technology
- Need for a mechanism to control the visibility of the built-in tool holder structure
- Automatic recognition & autonomous correction function/mechanism was
developed where vision and lighting module is built in on the tool holder enabling
on-machine measuring; automatic recognition of location and size of the specimen
for machining and the z-axis auto-focusing function enables autonomous
correction of the initial machining origin with 3-axis of width, length, and height to
suit the changed specimen (compares not only the width/length vision measuring
but also the thickness (height) of the material through visibility control)
- To create a completely automatic line linked structurally to ATC, an exclusive tool
for inserting into the tool (or chuck) holder and a hollow cylinder DSP board (designed
to prevent eccentric force to suit the spindle machining tool structure) for lighting
device control were developed, and the firmware software was developed, mounted,
and built into the machine.
- Regarding specification, CNC-linked autonomous identification function with the
degree of precision of 0.09 mm and the sampling time within 1ms and CNC-linked
auto-focusing control function were promoted to be applied.
- Integrated chuck holder built-in module structure, the machining origin
autonomous identification mechanism, and CNC-linked on-machine autonomous
correction functions are required
Technical Differentiation
- From the control aspects, 3-axis automatic identification measurement + Z-axis
auto-focusing, autonomous correction control mechanism are linked (CNC-linked)
- From the structural aspects, the remodeled machining tool holder built-in chuck
type is applied.
- From the mechanism aspects, the new concept of measurement identification and
correction control through the visibility and lighting control is introduced.
- From the interface aspects, wired/wireless data high-speed/high-resolution data
collection and filtering is possible.
- Vision measuring tool is made to be built into the device like the automatic tool
changer (ATC)
- The setup or the mounted location of the inserted processing product in the onmachine
is detected by mounting the vision device onto the tool holder.
- Machining origin automatic identification following change of the material is
supported to realize unmanned machining through allowing the actual machine to
judge and measure.
(Accuracy and productivity are improved by excluding human workers, reducing the
setup time, and minimizing the error occurrence.)
Distinctiveness |
Detail |
Current Global Status |
Goal of the Technology |
Functional Aspect |
CMeasurementhina |
Touch sensor (only measurement) |
Non-touch vision measurement and z-axis autofocusing (simultaneous measurement + correction) |
Applicable machining |
FMC machining |
Both FMC/RMC machining |
Related commercial items/ flexibility |
No commercial item/No flexibility |
Possibility of application, commercialization/removable design (original) response 1:N machining possible |
Method |
Operational aspect |
Semi-automatic |
ACTIVE TYPE Automatic and autonomous |

Excellence of Technology
- The automatic machine tool automatically identifies the machining origin for initial
machining (diversification of material) and reprocessing of existing processed
product to rid of the time required for setting the machining origin at the jog mode
for various forms and improve the setting accuracy of existing automatic machine
tool that depend on the initial setting; productivity is enhanced through separate
settings set automatically.
- Excellence of the technology has been proven by publishing (1 author) several SCIlevel
papers related or based on the technology on IEEE-ASME TRANSACTIONS ON
MECHATRONICS (within top 5% of SCI), JMST, IJPEM, Key Eng. (published on SCIlevel
journals multiple times)
- Has over 20 years of research experience in machine tool intellectualization and IT
integration.
- Received the 2013 Minister of Science, ICT and Future Planning Award (Scientist of
the Month Award), 2012 Korea Society of Mechanical Engineers Baekbong Technology
Excellence Award, 2011 KIMM Academic Award, and 2007 ICROS Academic Award.
CURRENT INTELLECTUAL PROPERTY RIGHT STATUS
PATENT
- TBuilt-in Type Vision Measuring Tool for Autonomous Machining Origin Setting
(KR2013-0117848, US13/533061)/Item Positioning Device and Positioning Method
(KR1106575)/Calibration Flaw Specimen Production Method (KR1140422)
KNOW-HOW
- Machine-tools pattern-matching based machining-origin identification technology
for processing machining-material change
- Unmanned autonomous setup and measurement technology in machining process, etc.
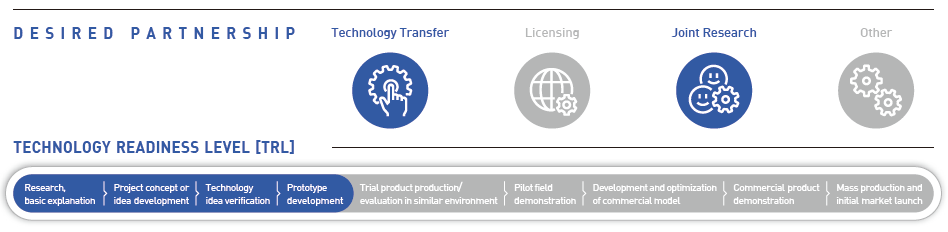
|